The powder coating process is a multi-step process. The process generally includes preparation, application, and curing stages. You will need at least a spray gun, a spray booth, and a curing oven for the coating process. Powder coating uses powdered material on a preheated substrate surface.
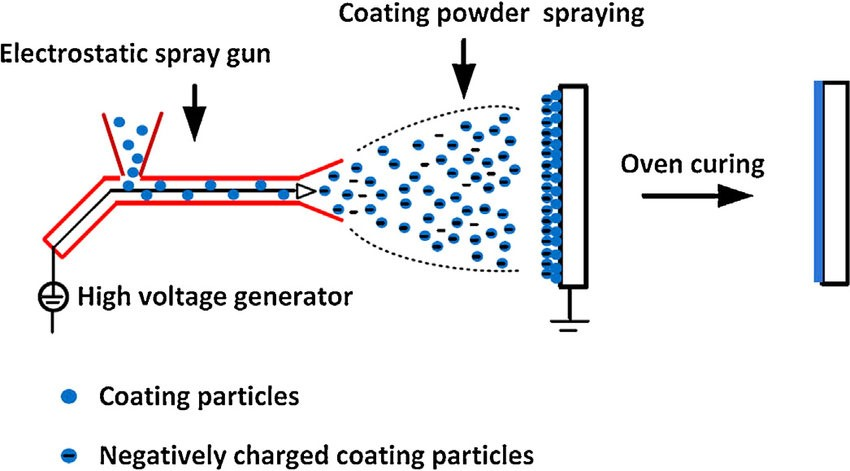
Here we will discuss the three main stages of obtaining a powder coating finish on machined parts.
Surface P[reparation Stage
Before any powder coating is applied, it is critical to clean and prepare the substrate surface. This is to ensure that the part is free of dirt, dust and debris. Inadequate substrate surface preparation may affect the adhesion of the coating powder to the part. It may also affect the overall quality of the finish.
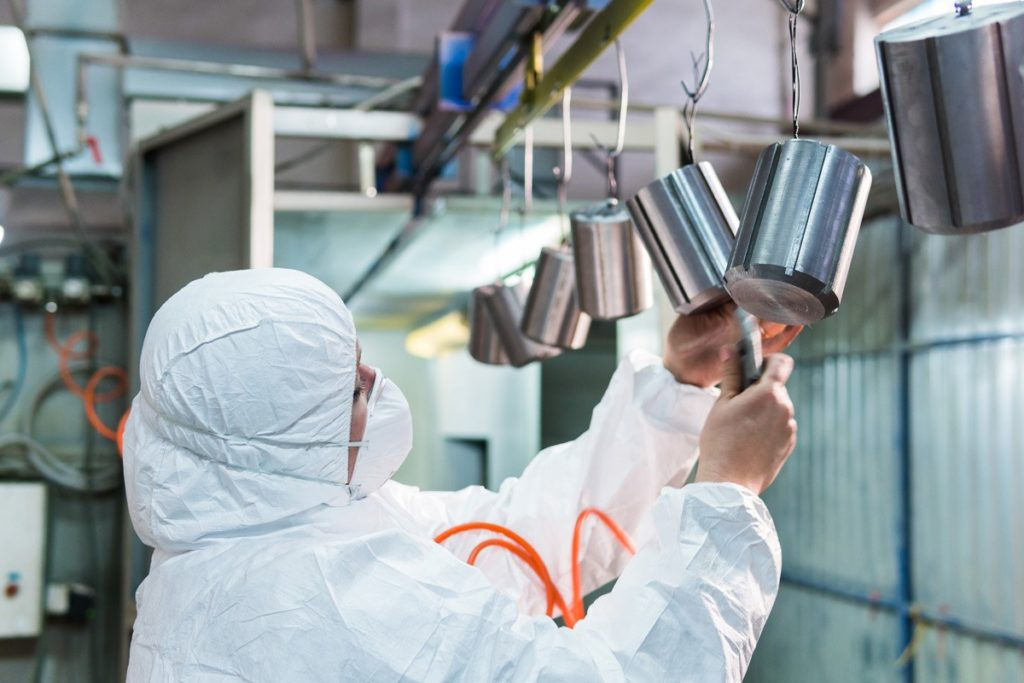
In the rapid prototyping industry, some of the steps in this phase include rising, cleaning, sandblasting, etching, and drying. In most cases, manufacturers use tools such as sandblasting rooms, cleaning stations, and drying ovens. Mild alkaline or neutral detergents in immersion tanks help remove grease, residues, or solvents from the surface of the part.
On the other hand, a cleaning station can also come in handy. This equipment can spray the parts with water, detergent or other pre-treatment solutions. It can thus help to chemically prepare or clean the surface before the powder coating process.
Additionally, a sandblasting booth may be necessary for parts that have surface debris such as scale or other similar defects. It could be injection molding defects or those from things like welding.
A blasting room uses a pressurized fluid (usually compressed air) in an enclosure to propel an abrasive against the surface of a part. The abrasive material can be grit, sand, or shot. As a result, the abrasive removes surface debris and creates a cleaner and smoother surface to apply the powder coat finish. A drying oven also helps evaporate water or solutions from rinsing or washing parts.
Powder Coating Stage
There are two main methods that manufacturers typically use for the powder coating process.
They are:
Electrostatic Deposition (ESD)
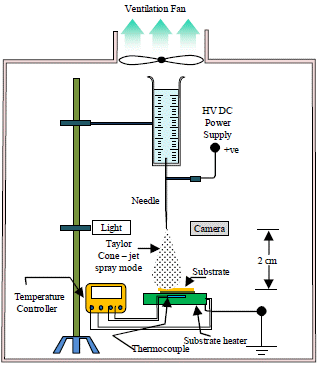
For your custom metal parts, the electrostatic spray deposition method helps apply the coating material. This application uses a powder feeder, a powder spray booth, and an electrostatic spray gun. The spray booth is the work area where the powder material is applied to the part.
This area also acts as an air filter and overspray container. In this method, the spray gun applies an electrical charge to the fluidized powder material before applying to the substrate. With ESD, you can collect any overspray material using a specialized recovery system. These materials can be reused for future powder coatings.
Fluidized Bed Powder Coating
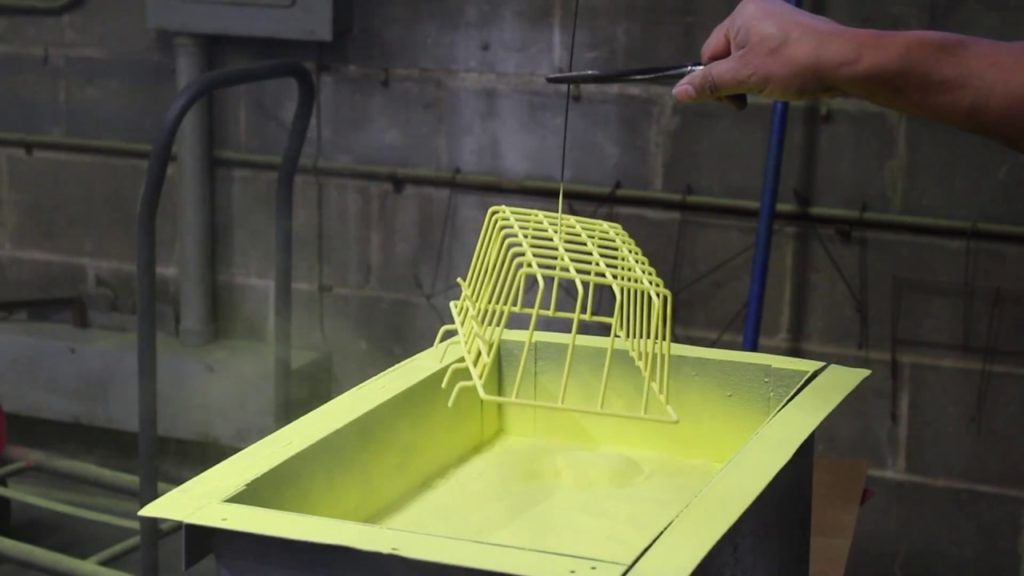
In this case, the first step is to preheat the parts to be coated and then immerse them in the powder material in a fluidized bed. Sometimes, charged powder particles can be introduced before the parts pass through the fluidized bed.
Coated Parts Curing Stage
The characteristics and particularities of the curing phase of powder coating depend on the method used. For ESD coated parts, curing must be performed in a powder curing oven. The temperature and time used for curing will depend on the size, thickness, and shape of the part. Typically, oven temperatures between 325 and 450 degrees Fahrenheit require curing times ranging from ten minutes to about an hour. Therefore, smaller machined parts will require less curing time and less heated air for proper curing. On the other hand, preheating of parts using fluidized bed curing provides an excellent curing environment.
In any case, assembly, packaging, and shipping of powder coated parts can be completed when they are cool enough to be handled.