Generally speaking, we have three major categories of powder coatings, applied to metal or plastic parts. Often, the costing and potential complexity of the powder coating process will dictate a manufacturer’s choice.
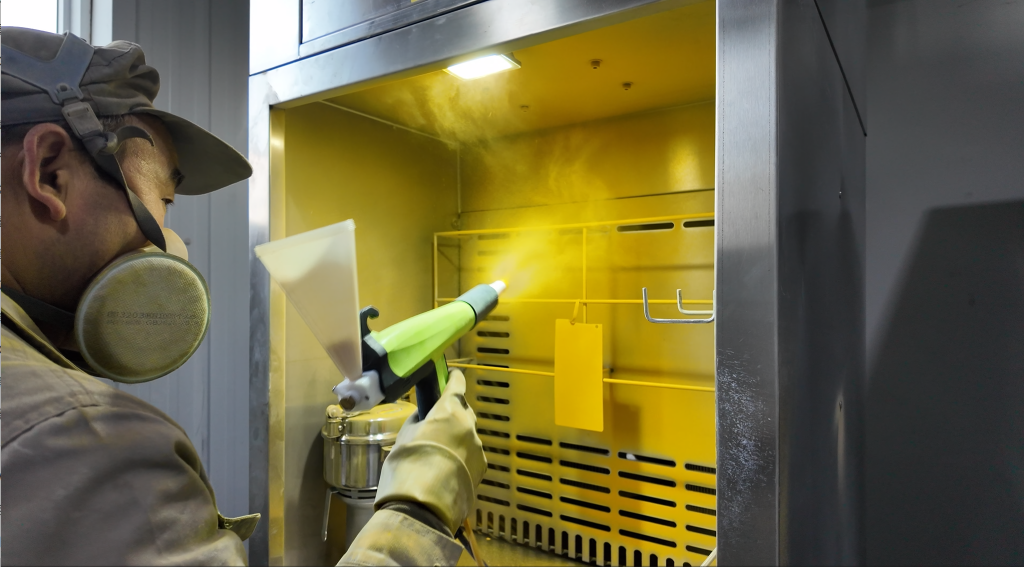
Within these categories of powder coatings, there are many subgroups. Furthermore, each powder is designed to achieve a specific finishing quality. Types of powder coatings include:
1.Thermoplastic powder coating finish material
These are synthetic materials that are capable of forming a variety of structures. They melt at high temperatures and solidify when cooled. Thermoplastic materials coat metal parts by melting at the application temperature. They then exhibit increased chemical and mechanical strength when cooled. In the prototyping industry, these powder coating materials are popular for their durability and aesthetic benefits. Some of them include:
Polyvinyl Chloride (PVC) Powder Coating
When you are looking for a durable and smooth powder coating for your parts, you should choose PVC coatings. These coatings are flexible and suitable for a wide range of applications. They are also resistant to many solvents, impacts, and sprays. PVC coatings have good dielectric strength, making them suitable for electrical applications.
Polyester Powder Coating
These coatings look great, resist wear and tear, and they also weather well. They are great for exposed car parts like strut springs. You'll find them in a variety of color pallets. They are strong, tear-resistant, and reduce shrinkage.
Nylon Powder Coating
Nylon powder coatings are very durable and they impart resistance to the material. They provide adequate protection against solvents and chemicals, ensuring a longer service life for the parts. Nylon is valuable as a coating material for gears and conveyor components due to its low coefficient of friction.
Polyolefin Powder Coating
Powder coatings of polyolefin materials are very resistant to chemicals and abrasion. These materials provide a smoother surface and excellent bonding characteristics for machine parts. Therefore, the medical industry can benefit from these coatings on laboratory components that require regular cleaning.
2.Thermosetting Powder Coating Finishing Materials
You apply thermoset powder coatings in a similar manner to thermoplastic powders. The difference, however, is that thermosets undergo a chemical cross-linking reaction. These reactions are generally irreversible when baked.
When cross-linking occurs, the physical properties of the plastic change. As a result, these changes cause these plastics to harden into a solid coating. Many times, thermosets are more difficult to cure than thermoplastics. Additionally, some of them can become brittle when hardened, especially in thicker coatings. Examples of these powder coating finish materials include:
Epoxy Resin
Materials coated with epoxy are generally hard and electrically insulating. However, when you expose them to UV light, they become brittle and can become dull over time. Therefore, most epoxy-coated parts are limited to indoor use or underground applications, such as pipes.
Epoxy Polyester Hybrid
This blend creates a softer plastic by adding polyester to epoxy, which helps prevent chipping or cracking. Hybrid powder coatings perform better outdoors than regular epoxy coatings. This is because they have better weathering capabilities and less chalking.
Acrylic Powder Coating
Acrylics blend perfectly on the surface, leaving a high gloss finish that may be clear or tinted. Currently, they are used as automotive coatings for specific parts, such as exposed engine components and parts that require an ultra-glossy finish.
3.Ultraviolet (UV) Cured Powder Coat Finish Materials
Traditional powder coating processes use convection ovens or standard infrared to impart a powder coating finish. In this case, the temperature is often as high as 400 degrees Fahrenheit. In addition, the curing time can be about 10 to 30 minutes. Due to these factors, it is difficult to coat injection molded plastic parts with powder coating.
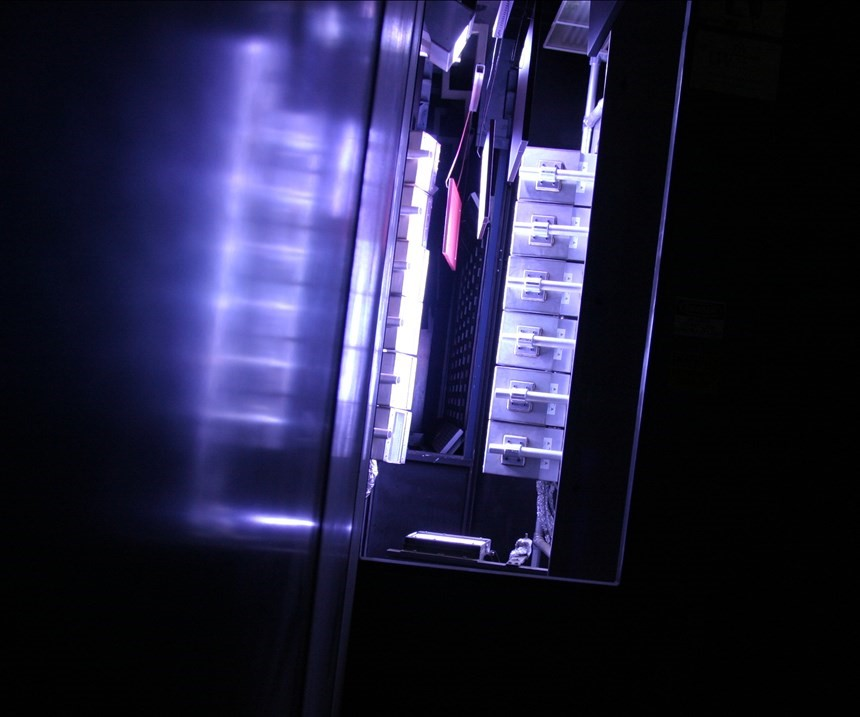
However, recent developments are creating new powders and resins. These resins use ultraviolet (UV) light to cure powder coated parts. UV light can be cured in two minutes at temperatures below 200 degrees Fahrenheit. As a result, plastic parts and other materials that may not withstand higher coating temperatures can be powder coated. Additionally, such coated prototypes can speed up time to market, thereby reducing manufacturing costs.